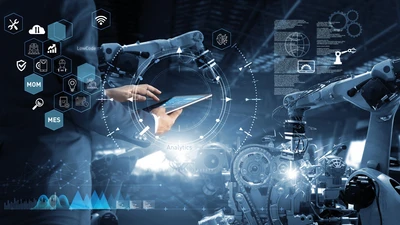
MES & MOM: Revolution in the shop floor
Manufacturing Execution Systems and Manufacturing Operations Management
Welcome to the world of Industry 4.0! Imagine a production floor where machines and people work in perfect harmony, supported by advanced technologies that monitor and optimize every step. Manufacturing Execution Systems (MES) and Manufacturing Operations Management systems (MOM) are the driving forces behind this revolution. They are transforming traditional factories into smart, connected production facilities that are not only more efficient, but also more flexible and transparent. Together, we will explore how these cutting-edge systems are shaping a new era of industrial production and the advantages they offer to companies and their employees.
What is an MES?
A Manufacturing Execution System (MES) is a software-based system that is used to monitor, document, control and optimize the entire production process – along the entire production chain from manufacturing to the final product and delivery. State-of-the-Art MES solutions are able to integrate the entire shop floor and all production data from various sources to provide a holistic overview of the production process and enable companies to react quickly to changes and problems. As a result, production processes can be improved, and the overall performance of the company increased. An MES can be defined as a bridge between the operational control systems on the shop floor (e.g. SCADA, PLC) and the higher-level systems (e.g. ERP, PLM systems). The area of application is diverse: MES solutions serve the processes from goods receipt to goods issue. This means that they are also used in adjacent specialized departments, such as logistics, maintenance or to provide operational and strategic data at C-level.
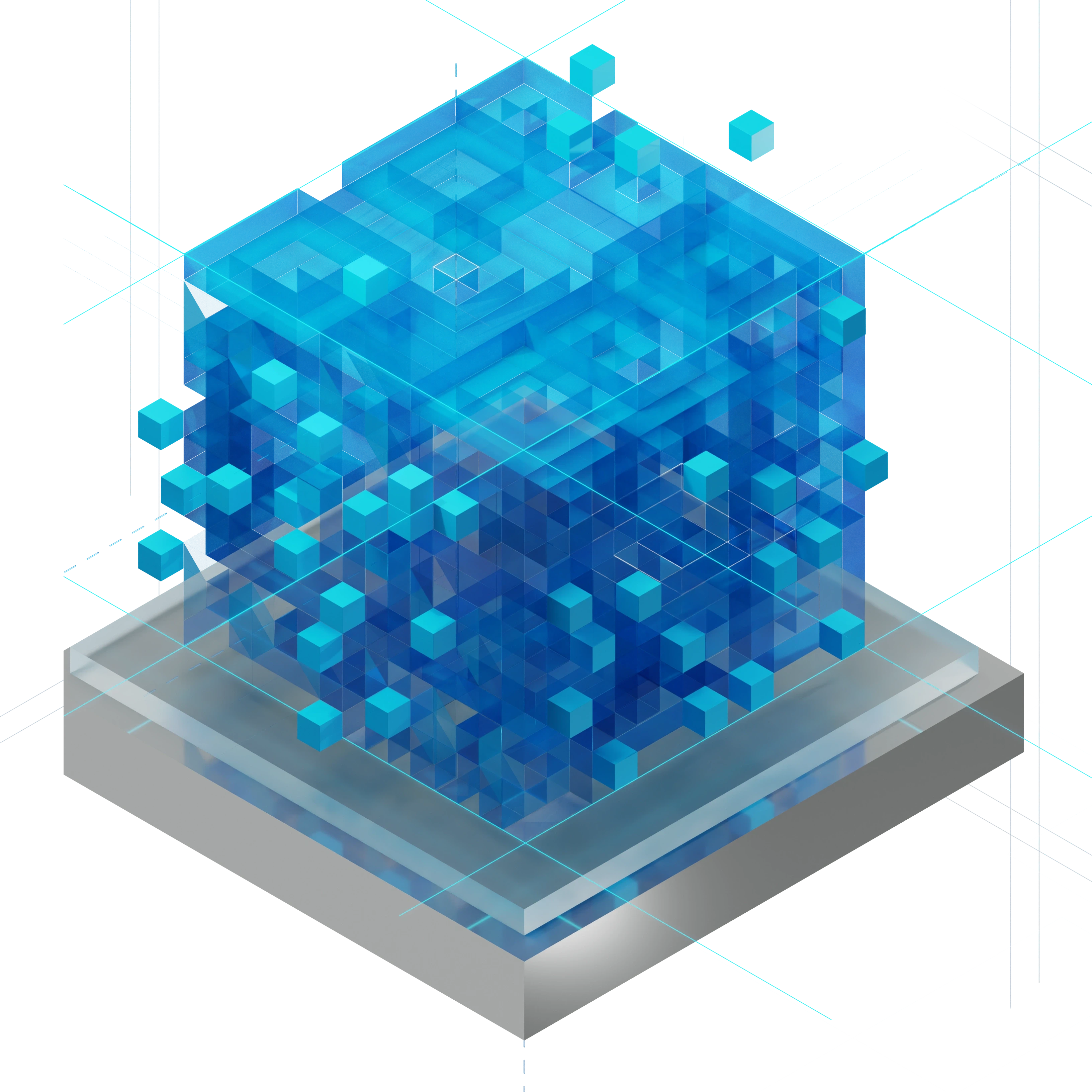
How does an MES software work?
The MES facilitates the decision-making process regarding the allocation of production tasks to machines, systems, lines, etc. It also determines the optimal combination of operating resources and tools for each task. As a functional layer between the machines on the operational level (Operational Technology, or "OT" level for short) and the administration or the Enterprise Resource Planning System, ERP, (IT level), the MES software provides the management with data that is required for timely decisions, production control and transparency in real time, as well as for process optimization.
To guarantee product quality, quality checks can be scheduled, conducted and their outcomes documented in the MES. The control, monitoring and automation of processes on the shop floor is independent of location: a modern MES allows digital access to critical real-time information from production at any time via smartphone or tablet.
Today, MES solutions are indispensable for efficient production processes. The ever-increasing demands on profitability and flexibility as well as the constantly changing production environments make the use of an MES essential. In a nutshell, MES solutions offer real-time monitoring and control of production processes and help to increase efficiency, reduce production costs and improve product quality.
What is a MOM?
Manufacturing Operations Management (MOM) software is a further development of the MES solutions described above. MOM can be described as an overarching concept that integrates the production processes of the MES into the business processes of overall value creation. The MES is therefore an important part of the MOM approach and focuses on use on the shop floor and the tasks and processes within production, while a MOM also organizes and coordinates information across different areas of the company. In addition to the executing MES functions, the concept also includes adjacent functions from the areas of ERP, PLM, QMS and IIoT.
- Product Lifecycle Management (PLM): Product development and planning of production steps
- Enterprise Ressource Planning (ERP): Sales planning and commercial processing of orders
- Manufacturing Execution Systems (MES): Execution of production orders
- Quality Management Software (QMS): Ensuring product quality
- Industrial Internet of Things (IIoT)-Plattform: Merging data from machine control and sensor technology and monitoring production processes in real time
Manufacturing operations management (MOM) can be described as a comprehensive concept for optimizing the entire value creation process. Companies achieve this optimization through the digital management of their manufacturing processes and the provision of specific and cross-divisional information. To ensure seamless communication from the production level to the management level, there is an exchange of information between the various IT systems.
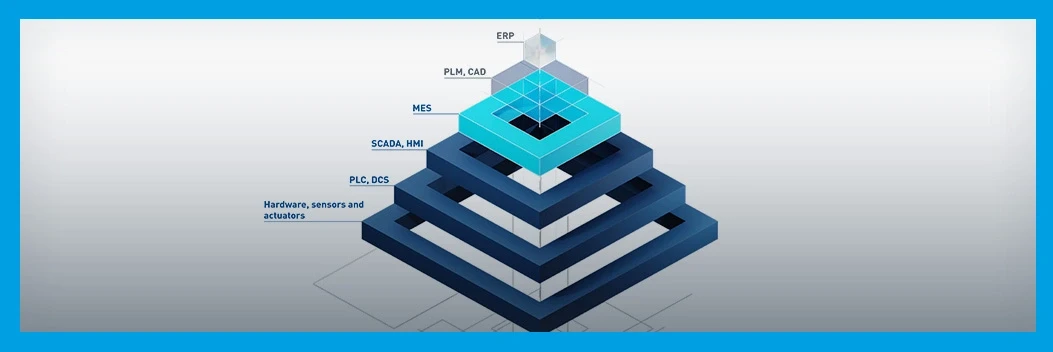
From MES to MOM: The difference
While an MES is specifically designed for real-time control and monitoring of production processes, a MOM system offers a holistic management solution – integrating a wider range of functions and modules to optimize the entire production environment even more comprehensively. The key difference is that an MES is mainly limited to monitoring and analyzing processes on the shop floor. MOM software, on the other hand, has a broader scope of application that extends across adjacent sectors.
Architecture
Manufacturing Execution Systems (MES) and Manufacturing Operations Management systems (MOM) are central components of modern manufacturing industries that aim to make production processes more efficient and transparent. The architecture of these systems is service-orientated and functionally multi-layered, as they must ensure integration and interoperability between different levels of the production chain.
The architecture of MES/MOM is a reciprocal interplay of different technologies and levels that enables effective and efficient production control. By integrating real-time data, standardized interfaces and analysis methods, production facilities can prepare for the challenges of a dynamic manufacturing environment.
Is installed in a data center within the end user's company premises.
Hosting takes place on a cloud infrastructure outside the company.
Is specially designed and optimized for use in cloud environments. The use of microservices enables flexible, scalable and more resilient production control and monitoring.
Advantages and benefits of MOM
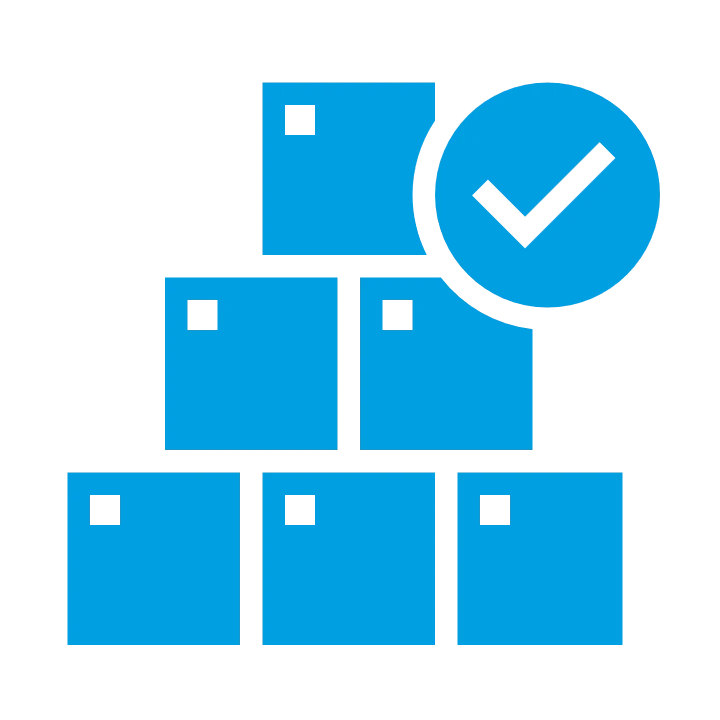
A modular, flexible structure based on standards
A key advantage of modern manufacturing technology using MOM-software is the independent microservices that enable customized configuration. These microservices offer the flexibility to activate or deactivate specific functions as required – allowing individual adaptation to the respective production requirements. Event-based communication facilitates the flow of information and allows data and results to be exchanged in real time. Seamless integration with other central systems such as ERP (Enterprise Resource Planning) also plays a key role. By linking manufacturing and business software, data and resources can be managed more efficiently. The result is improved overall performance and increased competitiveness.
Compliance with legal requirements
Effective control is an essential aspect of complying with the multitude of regulations that apply to manufacturers. MOM solutions can not only increase efficiency in a production facility, but also reduce the risk of fines, e.g. due to lack of compliance with logging and other costly measures. The latest security standards ensure confidentiality, integrity and data availability and provide reliable protection against unauthorized access and cyber-attacks. Especially in view of the EU's new cyber security directive, a holistic approach to IT-security is essential. A MOM system that already takes security aspects into account in the architecture and software design is an important tool for this.
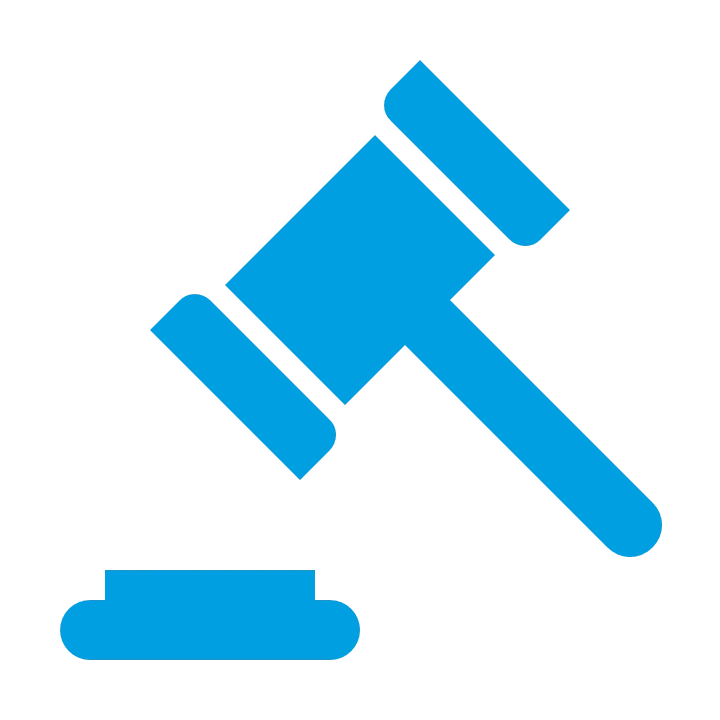
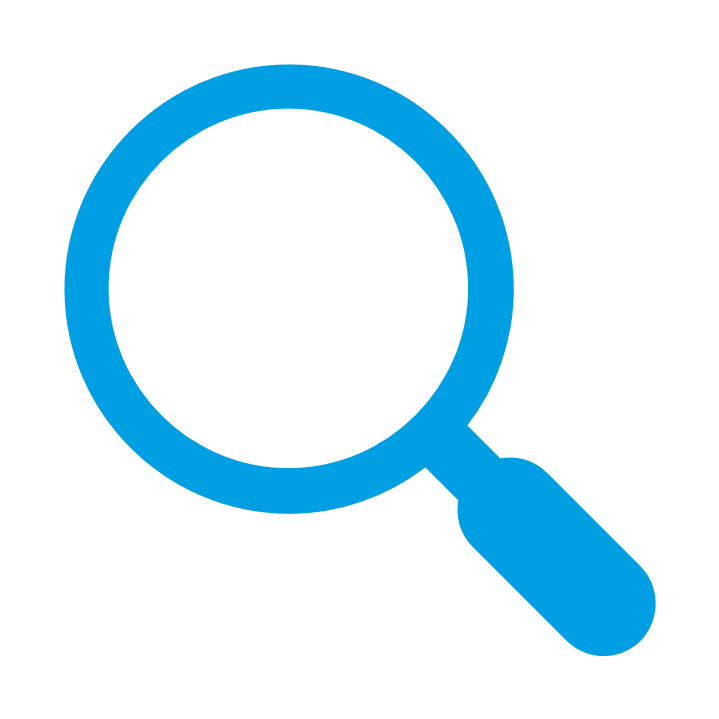
Transparency and control throughout the entire production process
Performance monitoring provides real-time insights into system performance, component interactions and data flows. The integration of a single sign-on enables flexible and secure login. Values and logs are collected, processed and visualized. Interactive dashboards and real-time diagrams are used to monitor key performance indicators such as OEE, which can be selected individually.
Shopfloor data acquisition documents all relevant key production figures in real time. In addition to recording, it also enables the verification and documentation of material data. A graphical evaluation of the system performance provides the corresponding visualization.
Increasing productivity and efficiency
By digitalizing work processes and optimizing production monitoring, manufacturers can identify and eliminate the causes of quality problems. MOM systems not only contribute to the optimization of production quality, but also enable the monitoring of warehousing and inventory management.
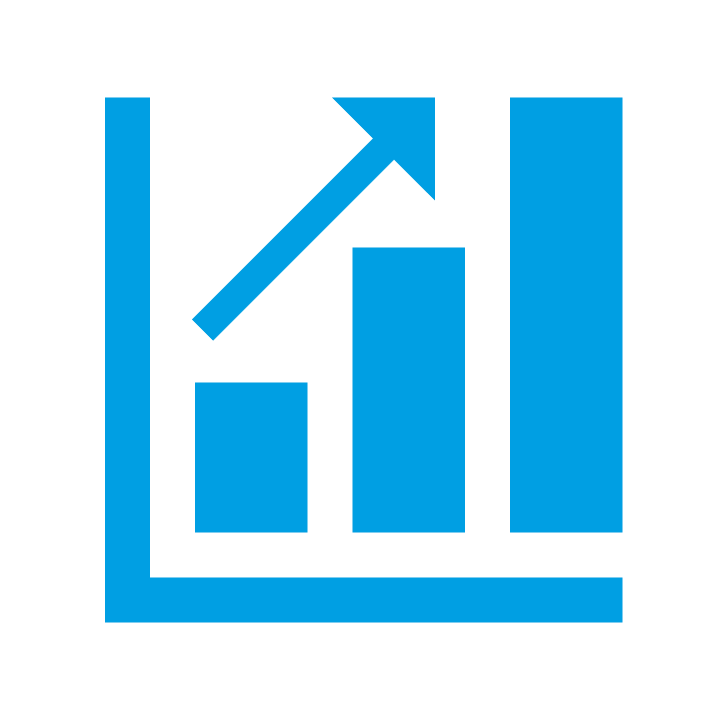
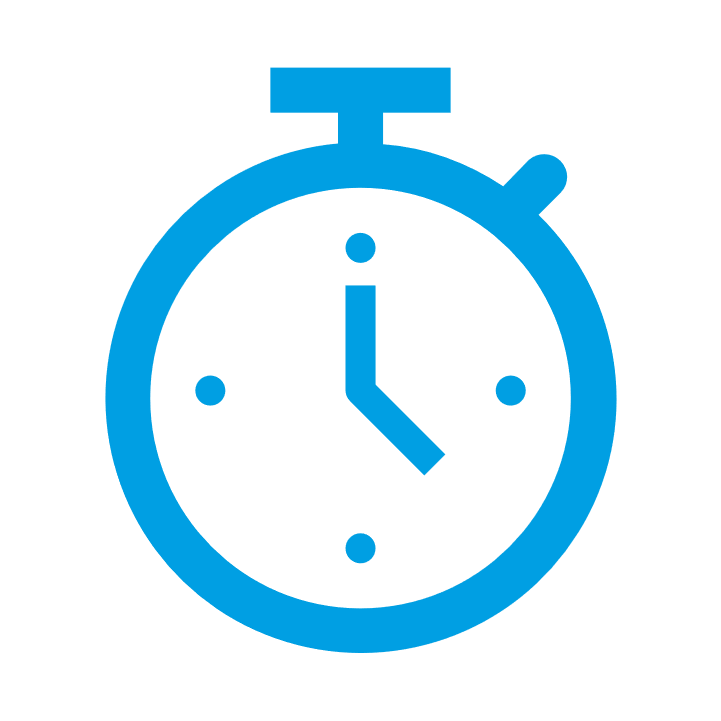
Reduction of Time-To-Market
The traceability, production planning and control functionalities are still essential, but have been expanded to include new applications, including AI and low-code methods. This results in a flexible yet highly standardized system that is also fully scalable and easy to roll out thanks to its template properties. Modern technology relies on independent microservices that enable customized configuration. Event-based communication via a message broker considerably simplifies the flow of information. Integration with other centralized systems such as ERP (Enterprise Resource Planning) is also guaranteed.
Control and monitoring of production in real time
Production-process control includes the management and planning of production orders using APS, resource allocation (personnel, materials, tools, etc.) and scheduling as well as real-time control of process management through bidirectional integration into the shopfloor. The availability of machines and materials is also optimized to ensure a smooth production process.
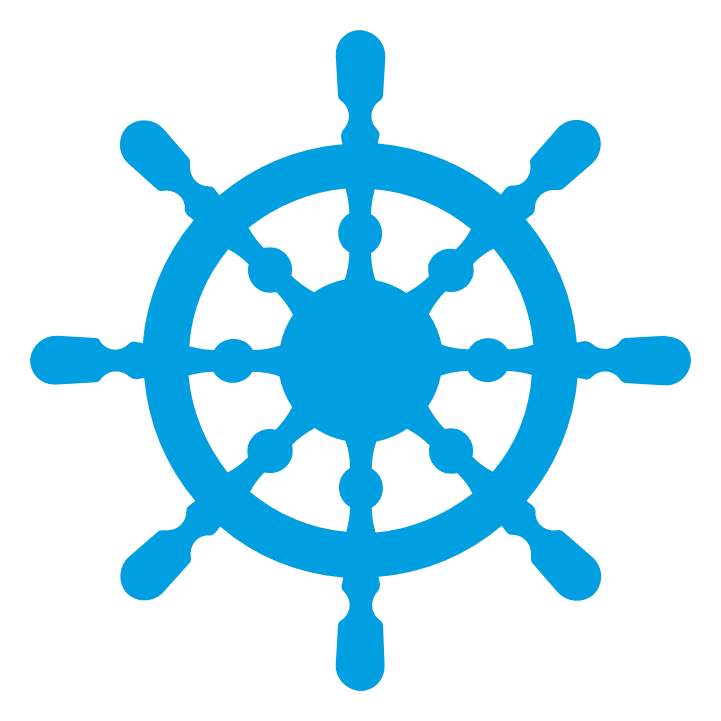
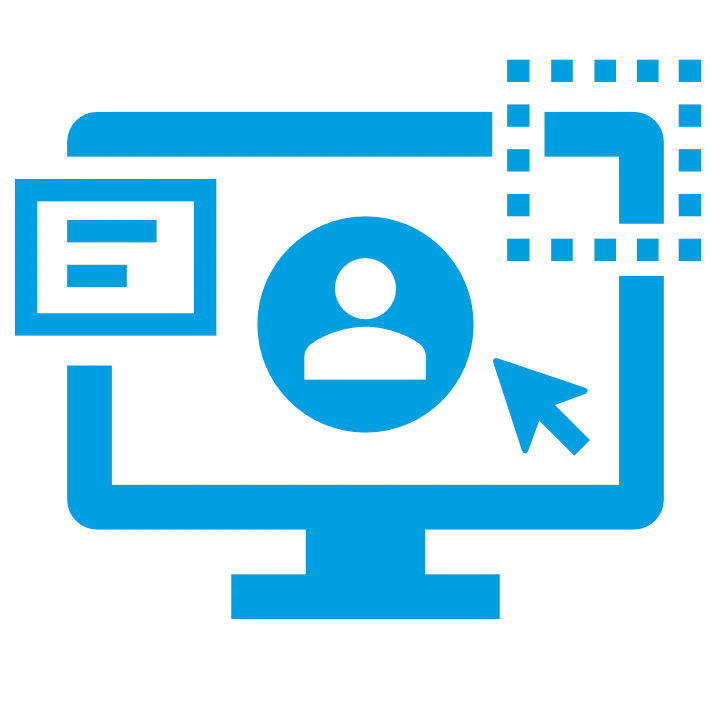
Intuitive and simple user interface
The state-of-the-art design provides a uniform visualization for all applications in the iTAC.Workbench. It uses a user-friendly HTML5 client framework and enables a customizable user interface that also supports the integration of third-party modules.
Would you like to find out more about our MOM solution?
In the modern manufacturing industry, MES and MOM are indispensable tools for remaining competitive. They not only offer comprehensive control and optimization of production processes, but also the necessary flexibility to react quickly to changes in the market. The future of manufacturing is digital, and MES/MOM solutions are the key to this future. Find out more here or get in touch with us. We look forward to hearing from you!
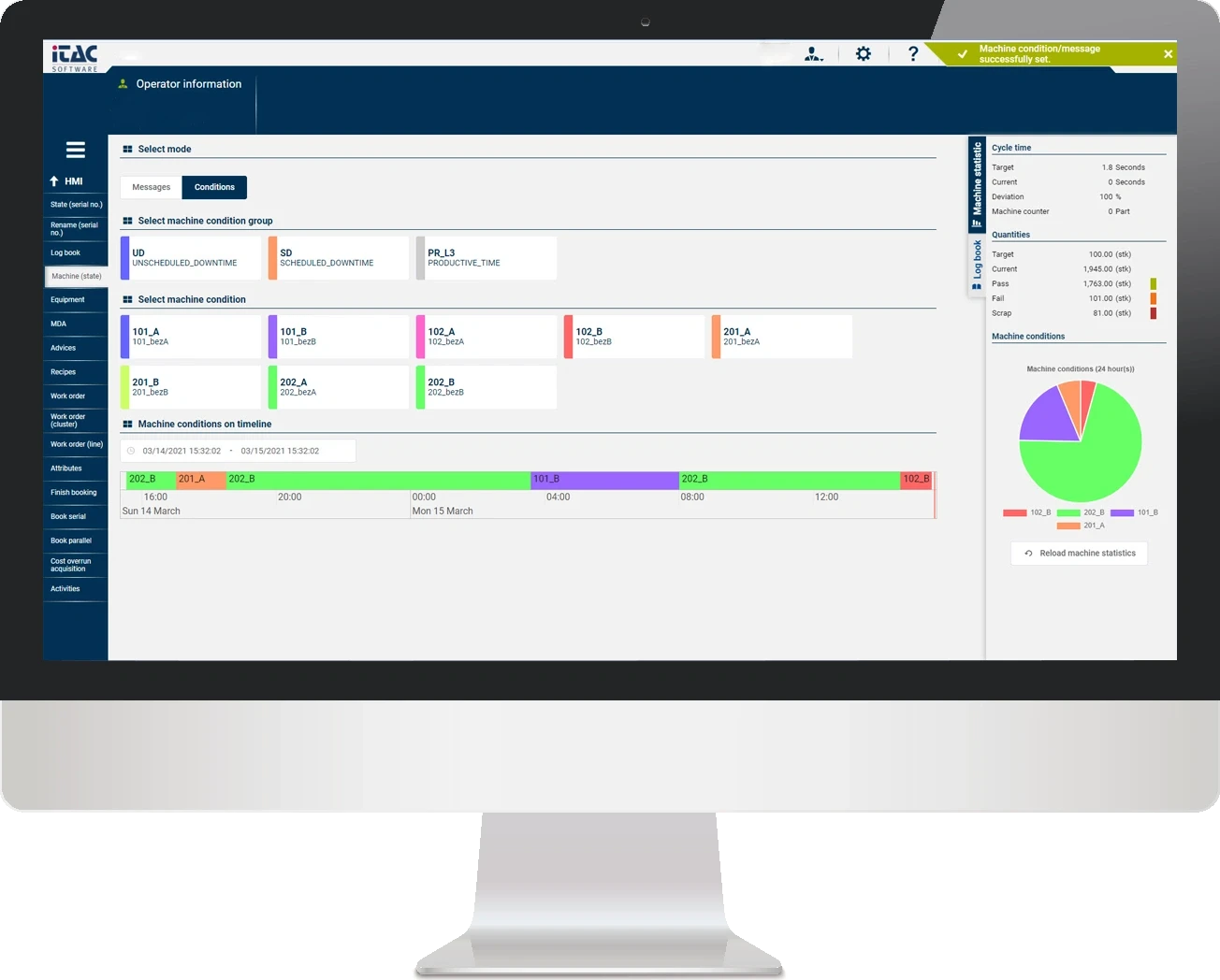