Battery Production
The electric car battery is the centrepiece of an electric car, which serves as the energy source for the drive system – because without the right battery system, an electric car would be useless. These electric car batteries consist of interconnected modules made up of battery cells. The cells are based on a lithium-ion technology, which guarantees a high energy density and therefore a long service life and enables a high number of charging cycles. Batteries are now regarded as a key technology in the field of e-mobility. They not only supply the electric motor with energy and electricity, but also other electrical systems in BEVs (battery electric vehicles).
The implementation of an intelligent software solution for controlling production, such as the iTAC.MOM.Suite, is therefore essential in order to optimize end-to-end manufacturing processes in battery production. Here, both the data in the "reel-to-reel" production of battery cells and the discrete data in the downstream assembly processes can be tracked. Manufacturers of rechargeable batteries and batteries, e.g. lithium-ion batteries,
are facing the challenge of converting their battery cell production to increased production capacities in order to keep up with current developments in the field of e-mobility. Some manufacturers are currently still often working with isolated solutions in IT production control that are focused on individual processes but do not represent a holistic solution for both upstream and downstream processes.
iTAC.MOM.Suite in battery production
The implementation of an intelligent IT solution, such as the iTAC.MOM.Suite, is essential for meeting the increasing demands of the market and fulfilling the most important criteria of battery production. It is a key factor in optimizing the manufacturing process. The entire production process is thus mapped in one solution, which means that individual lithium-ion battery production processes such as electrode production, cell assembly and cell finishing are interlinked across the entire system and process flows can be controlled and optimized holistically.
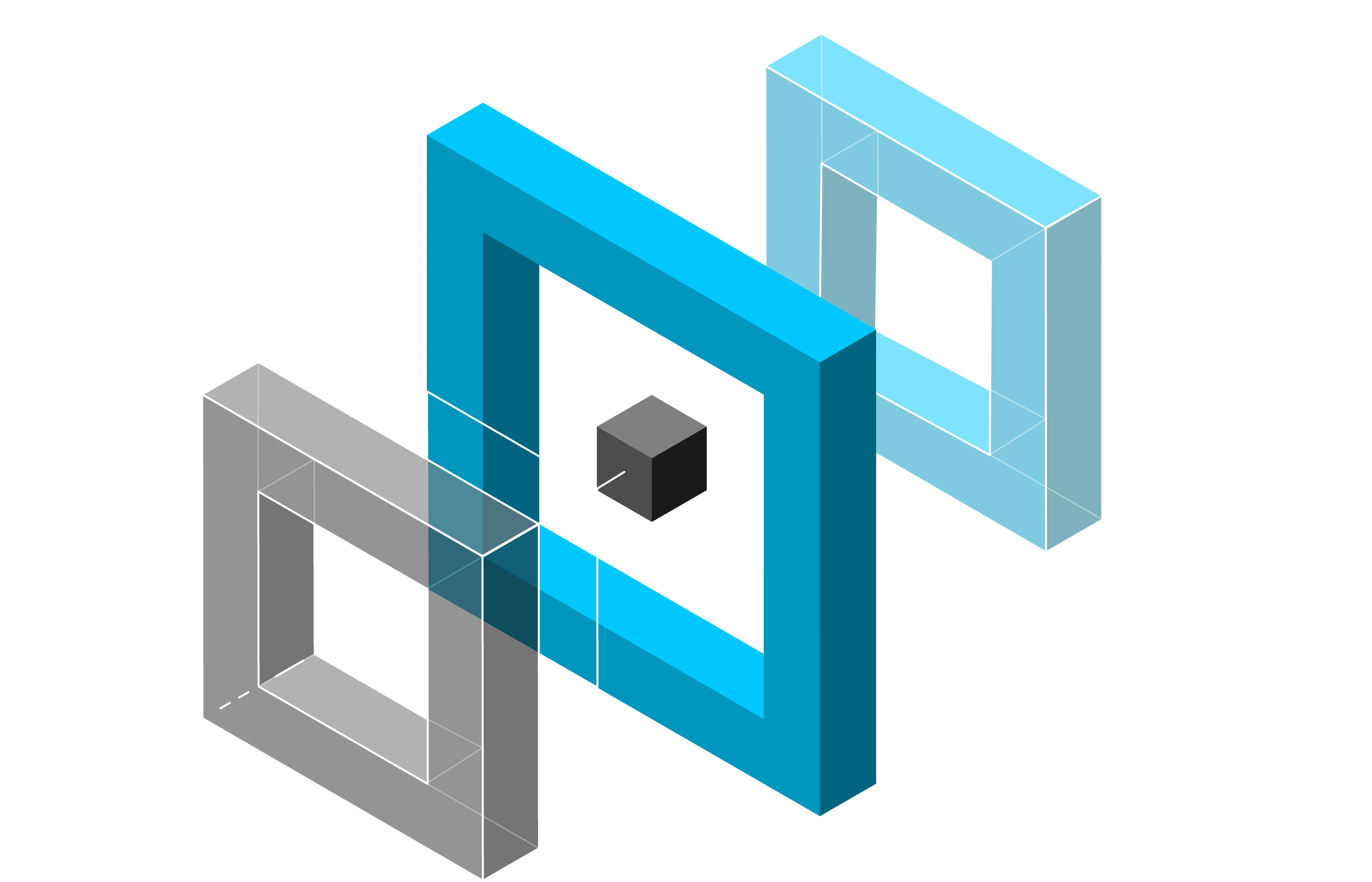
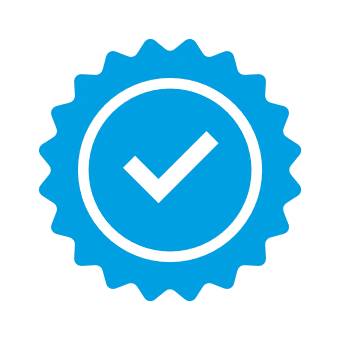
Continuous quality analysis and traceability are crucial in the battery manufacturing process in order to recognize and avoid errors at an early stage
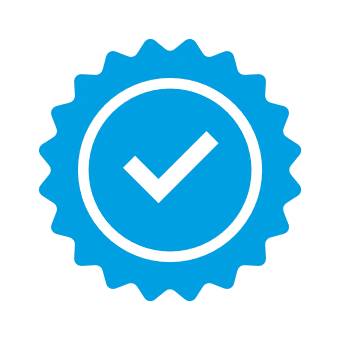
iTAC.MOM.Suite offers reporting tools such as iTAC.BI.Service, Quality Management and Production Management for analyzing and reporting process and quality data
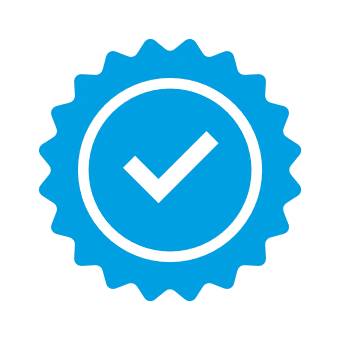
The solution supports the control of the entire battery cell production process, including electrode production, cell assembly and cell finishing
Useful information
In the battery cell manufacturing process, end-to-end quality analysis and traceability are extremely important to recognize and avoid errors in the production process at an early stage. The manufacturing reporting of the iTAC.MOM.Suite, such as the iTAC.BI.Service and Quality Management, provide analysis and reporting options for all product and process-related data. This enables the quality of the electrodes to be evaluated and analyzed throughout the entire process. Defects, such as holes or inclusions when coating the foils, are documented, can be tracked and thus sorted out in later process steps. As an end-to-end solution, the iTAC.MOM.Suite supports the control of all production processes from electrode production and cell assembly to cell finishing. In addition to the lithium-ion battery cell (with the dominant cell formats cylindrical, prismatic and pouch), production processes for other cell types can also be mapped in the MES/MOM solution. The solution is also used for the manufacturing process of hydrogen fuel cells.
In the highly complex production processes for electric car batteries, manufacturers rely on continuous controls and quality checks. Data is recorded, evaluated and checked for errors. The iTAC.MA.Suite can be used as a supplement to the iTAC.MOM.Suite or as a stand-alone solution to recognize changes and anomalies in the processes at an early stage and avoid errors. The Manufacturing Analytics Control product line offers analyses at machine, line and factory level and thus covers the entire spectrum of analytics.
The iTAC.MA.Suite is designed to analyze and optimize manufacturing performance and predict future process quality using analytics tools such as the iTAC.IIoT.Edge. The iTAC solution uses AI with mathematical algorithms to analyze the relevant information from the collected data so that predictions about processes and their changes can be derived. The battery cell production process is thus analyzed and controlled in real time in order to react immediately to disruptions in the production line. With the right data collection, data analysis, predictive maintenance and predictive quality tools, challenges associated with increased production capacity in battery manufacturing can be overcome in a targeted manner. This focuses on maximizing output while simultaneously maximizing quality. The iTAC.MA.Suite forms the correlations between the different process data and can therefore visualize the final impact of different anomalies in real time.
The production of batteries plays a central role in the ever-evolving world of electromobility. In electric cars, batteries and accumulators are at the heart of the drive system, supplying the vehicle with the energy it needs. Long-lasting battery systems are crucial to maximizing the range and performance of electric cars. However, the growing electromobility market also presents manufacturers and suppliers with new challenges in production. Battery cell production requires precise processes and high-tech production facilities. The task is to use resources and raw materials sparingly and efficiently and to firmly establish and further develop the new generation of e-car models. The reduction of CO2 emissions and the use of low-CO2 production processes are important goals. The materials should be processed using innovative production methods and ensure a long service life for the electric car battery. Battery production is therefore a key component for the future of electromobility and plays a major role in paving the way for a sustainable and electric vehicle fleet.
Battery production begins with the manufacture of the cells that form the basic building block in the production of electric cars. Just as smartphones and laptops aim for a long battery life, it is also important for the lithium-ion battery in electric cars to provide the longest possible energy supply. Lithium-ion batteries are widely used as they offer a high energy density and therefore have a large capacity, which results in a long range for the electric car. These lithium-ion cells are made from materials such as cobalt, nickel, lithium and other metals, whereby the extraction of rare earths and the handling of CO2 emissions play an important role. The manufacturing companies are continuously working on the development of new batteries that offer higher performance and a longer service life to meet the requirements of the next generation of electric cars. The batteries are then assembled into packs or battery packs and installed in the vehicles. These battery packs provide the necessary energy for the electric motor that drives the car. Manufacturers of electric cars in the industry work closely with battery production specialists to ensure that the batteries meet the highest quality standards. In doing so, the companies utilize sound research expertise. Aspects of battery recycling are also becoming increasingly important in order to promote the sustainability of electromobility.
Would you like more information?
Find out more about the many possibilities of the iTAC.MOM.Suite in the field of battery manufacturing. Contact our team of specialists with a wide range of knowledge and expertise to discuss your requirements and how we can help you!
Highlights & Benefits

Optimized production planning (APS) based on actual and limited capacities

Process control and mapping of the entire production process in one solution (end-to-end)

Continuous traceability of all production steps

Compliance with quality and performance characteristics

Transparency in production with both business intelligence and real-time dashboarding

Full compliance with all standards and requirements (production compliance)

Exploitation of optimization potentials in increasing productivity through optimized production processes

Application of data analytics tools for predictive control of production processes

Performance management