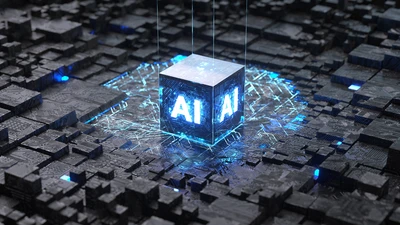
AI in manufacturing
Revolutionary transformation or just hype?
Artificial Intelligence (AI) – the buzzword of our time. However, it’s also a term that can lead to a great deal of confusion. It is no surprise that many decision-makers in companies, responsible for growth and success, often feel overwhelmed, thinking, “How am I supposed to make the right decisions? I’m not a data scientist!” Let’s clear up the confusion and break down where AI can be meaningfully applied in production. We will give you a heads-up: The role of artificial intelligence in the manufacturing industry goes far beyond a temporary trend or hype. It is already a reality in today’s factories, driving groundbreaking changes where it’s used effectively. Over the past few decades, AI has evolved from a futuristic concept to an essential tool that is pushing efficiency, quality, and flexibility in production to new heights. What sounded like science fiction yesterday is already becoming reality on factory floors today. This development does not just focus on improving efficiency but also aims at boosting product quality and flexibility in the manufacturing sector. The integration of AI in production promises to revolutionize how companies manage and optimize their processes. We outlined 10 key ways this is already happening using the example of an electronics production. This is also applicable to other industries.
Content
10 benefits of implementing AI in manufacturing processes
Anomaly detection
AI algorithms analyze images of PCB assemblies to detect patterns linked to common defects like soldering issues, misaligned components, and missing parts. These systems compare PCB images with predefined standards to spot anomalies. AI distinguishes between actual defects and false alarms, reducing unnecessary inspections and rework.
Benefits:
- Higher accuracy in defect detection
- Fewer false positives
- Faster inspection processes
- AI models continuously learn from new data, improving accuracy over time
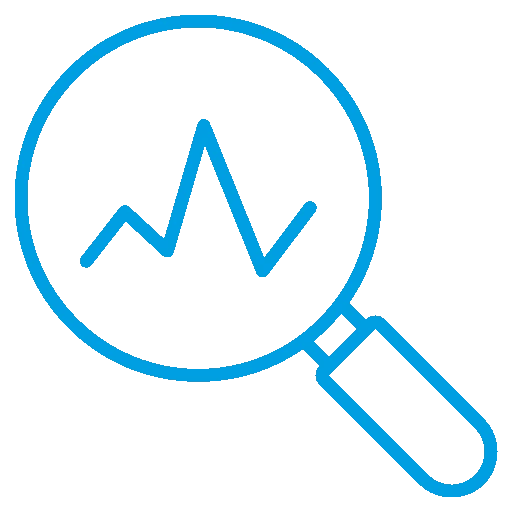
Real-time monitoring and alerts
AI systems enable real-time monitoring of production lines, allowing immediate intervention when quality issues arise. Alerts are triggered to address problems promptly.
Benefits:
- Instant intervention
- Reduced error rates
- Improved operator response times
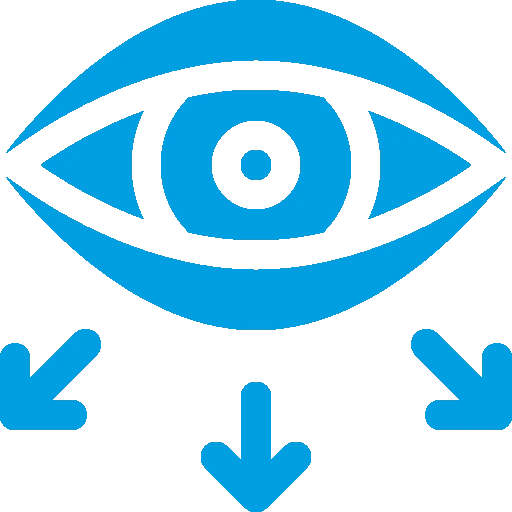
Tracking downtime (planned and unplanned)
AI tracks and analyzes machine performance to monitor both planned and unplanned downtimes, identifying causes and patterns.
Benefits:
- Better insights into downtime causes
- Proactive maintenance planning and minimized production interruptions
- Real-time event tracking enables quick identification and resolution of issues, improving overall equipment effectiveness (OEE)
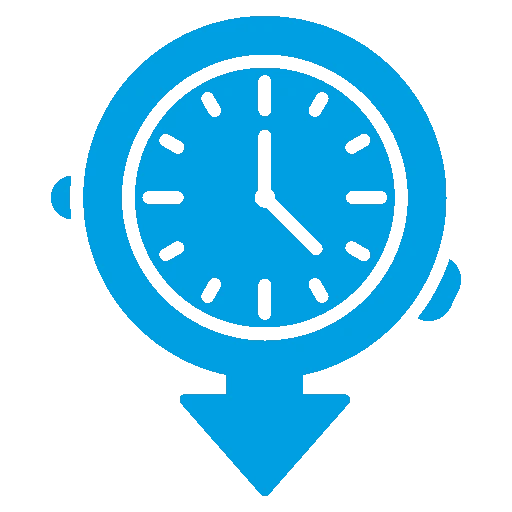
Predictive maintenance
AI analyzes production equipment data to predict when maintenance is needed, preventing unexpected breakdowns and reducing downtime. Early detection of equipment failures helps maintain consistent production quality.
Benefits:
- Reduced unexpected downtime
- Lower maintenance costs
- Extended machine lifespan
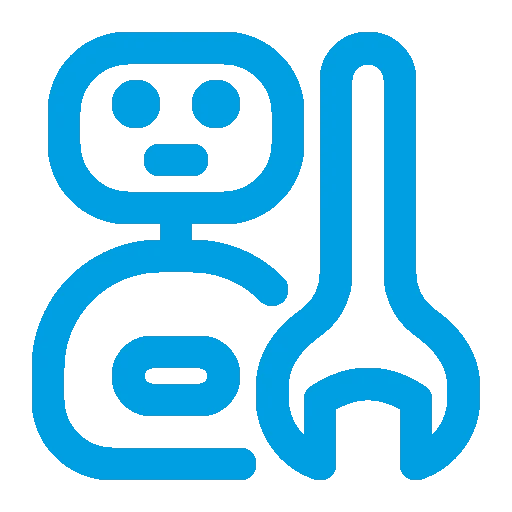
Quality control support
AI classifies types of defects, enabling more targeted corrective actions.
Benefit:
- Detailed defect analysis helps identify root causes and drive process improvements
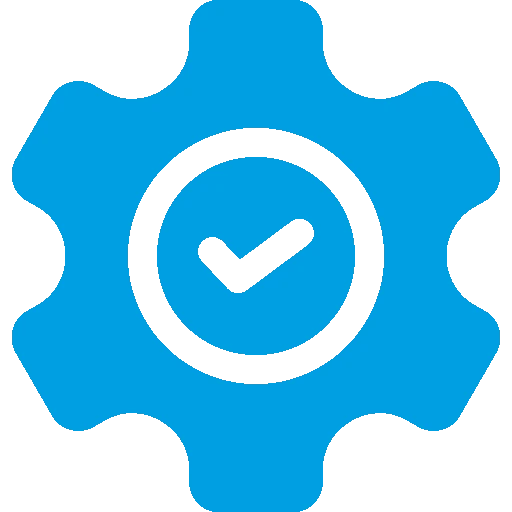
Data analysis
AI analyzes historical production data to uncover trends and correlations that may point to underlying quality issues.
Benefit:
- Insights from data analysis can lead to process adjustments and improvements
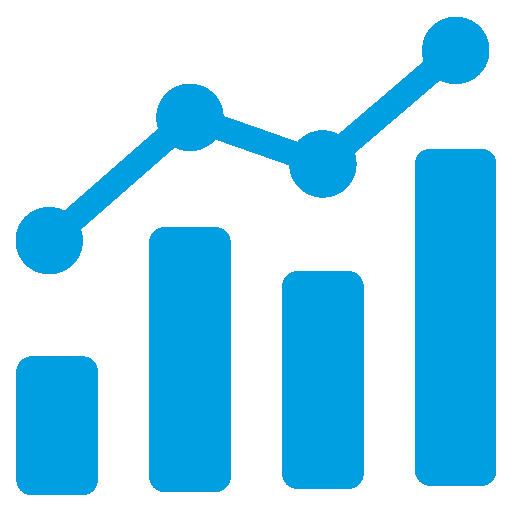
Process optimization
AI algorithms optimize production parameters like temperature, pressure, and timing to enhance overall product quality and yield.
Benefit:
- By continuously learning from production data, AI suggests optimal settings for different production runs
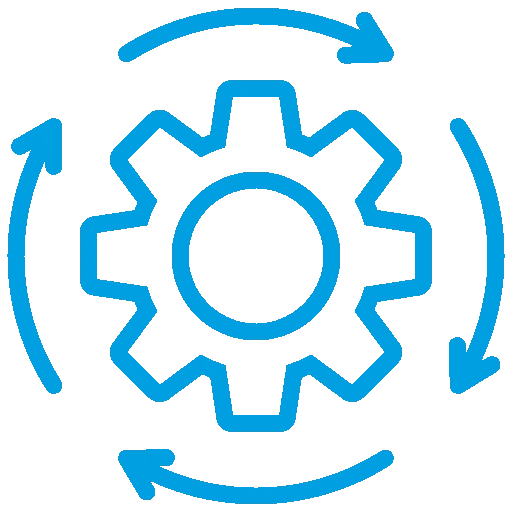
Supply chain management
AI improves supply chain efficiency by predicting material shortages, optimizing inventory, and ensuring timely delivery of components.
Benefit:
- Improved supply chain management directly impacts production quality and efficiency
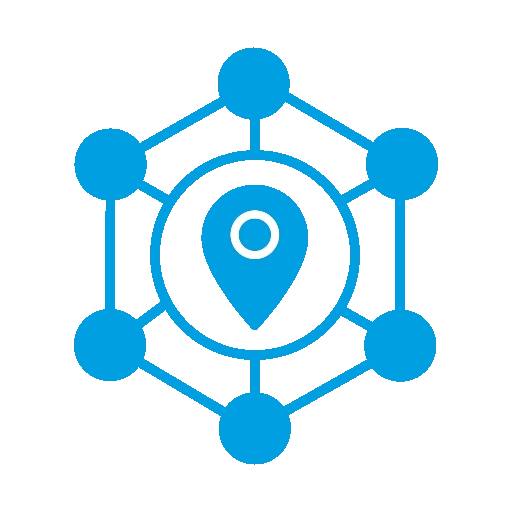
Ressource allocation
AI optimizes the allocation of human and machine resources, ensuring the right resources are available at the right time.
Benefit:
- Efficient resource allocation minimizes bottlenecks and maximizes throughput
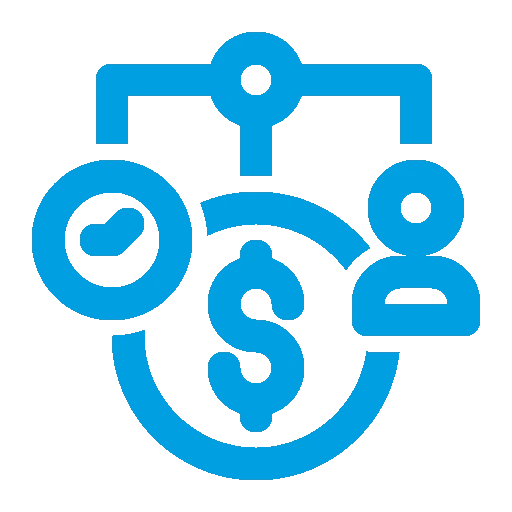
Overall Benefits
- Higher accuracy: Greater precision in defect detection compared to traditional methods
- Reduced scrap and rework: Early and accurate defect detection reduces waste and rework
- Cost savings: Lower operating costs through predictive maintenance and optimized resource utilization
- Increased efficiency: Improved throughput and yield via optimized processes and schedules
- Scalability: AI systems handle large data volumes and scale seamlessly with increasing production demands
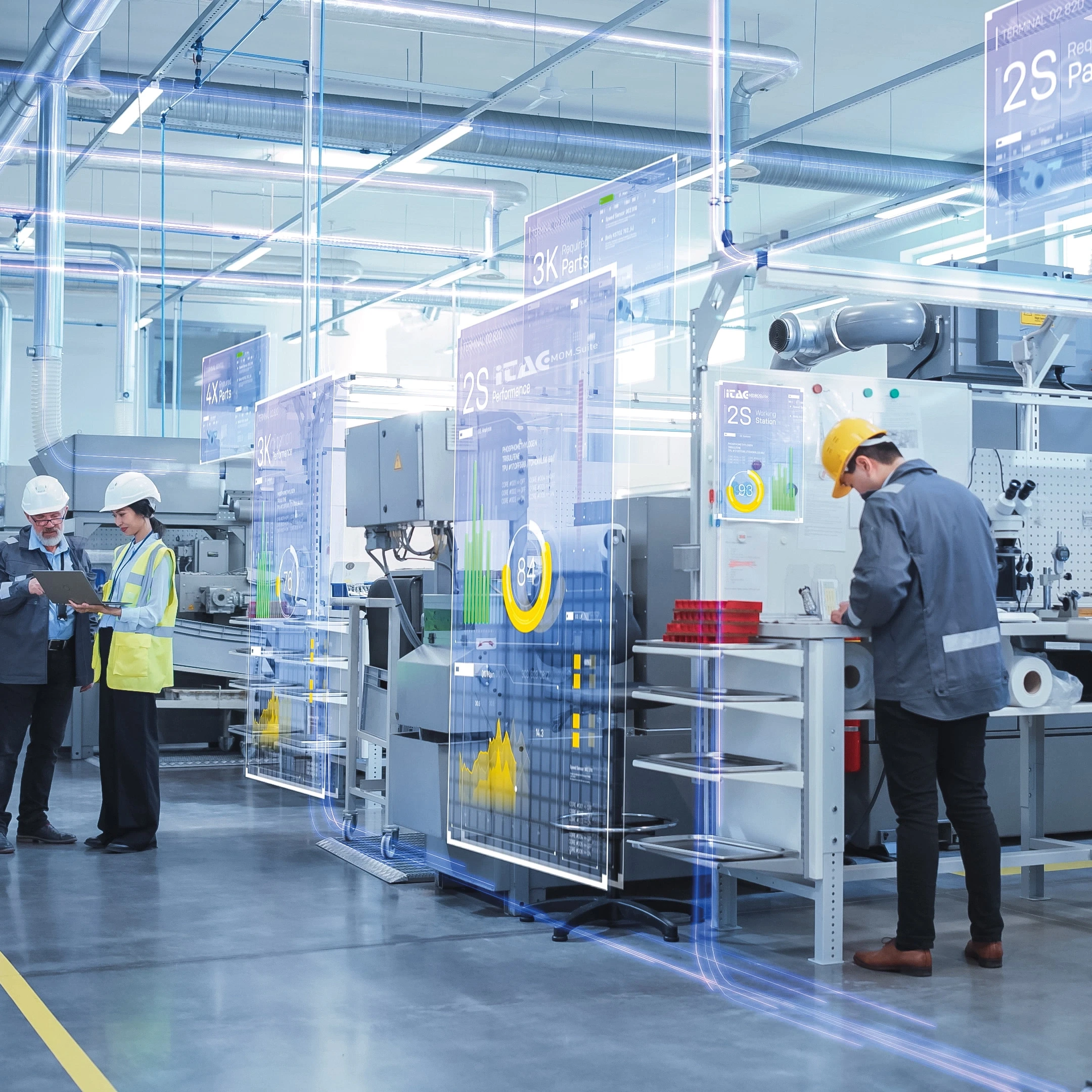
Areas of application of AI in manufacturing
The integration of Artificial Intelligence (AI) in production offers numerous applications that go far beyond simple automation. In the context of Industry 4.0, AI is revolutionizing the way production processes are managed, monitored, and optimized. Here are some of the key areas where AI is making a difference:
Intelligent robotics
AI-powered robots carry out complex tasks with precision and speed, adapting flexibly to different production requirements. This is particularly relevant in the electronics industry, where precision is critical.
Benefits:
- Higher precision and speed
- Flexibility and learning capabilities
Production planning and control
AI analyzes data to create optimal production plans, maximizing resource utilization. This is a central aspect of Industry 4.0, significantly boosting efficiency across industries.
Benefits:
- More efficient production control
- Better adaptation to changes in demand
Energy management
AI optimizes energy consumption in production facilities, identifying potential savings and reducing energy costs. This contributes to sustainability in the industry.
Benefits:
- Reduced energy consumption
- Cost savings
Human-machine collaboration
AI assists workers with complex tasks, improving productivity and safety in the workplace. In the electronics industry, this can significantly enhance both precision and efficiency.
Benefits:
- Increased productivity
- Enhanced workplace safety
Production simulation and modeling
AI creates virtual models of production processes to identify bottlenecks and test process improvements. This is particularly useful in electronics manufacturing, where accurate simulations are crucial.
Benefits:
- Identification of bottlenecks
- Risk minimization
Customized production
AI adjusts production processes in real-time to meet individual customer requirements, leading to higher customer satisfaction. This is a key advantage in the electronics industry, where customized solutions are in high demand.
Benefits:
- Higher customer satisfaction
- Flexibility in production
The applications of AI in production are diverse, offering tremendous potential for companies that embrace these technologies. Within the framework of Industry 4.0, artificial intelligence is the key to more efficient, flexible, and sustainable production across industries, especially in electronics manufacturing.
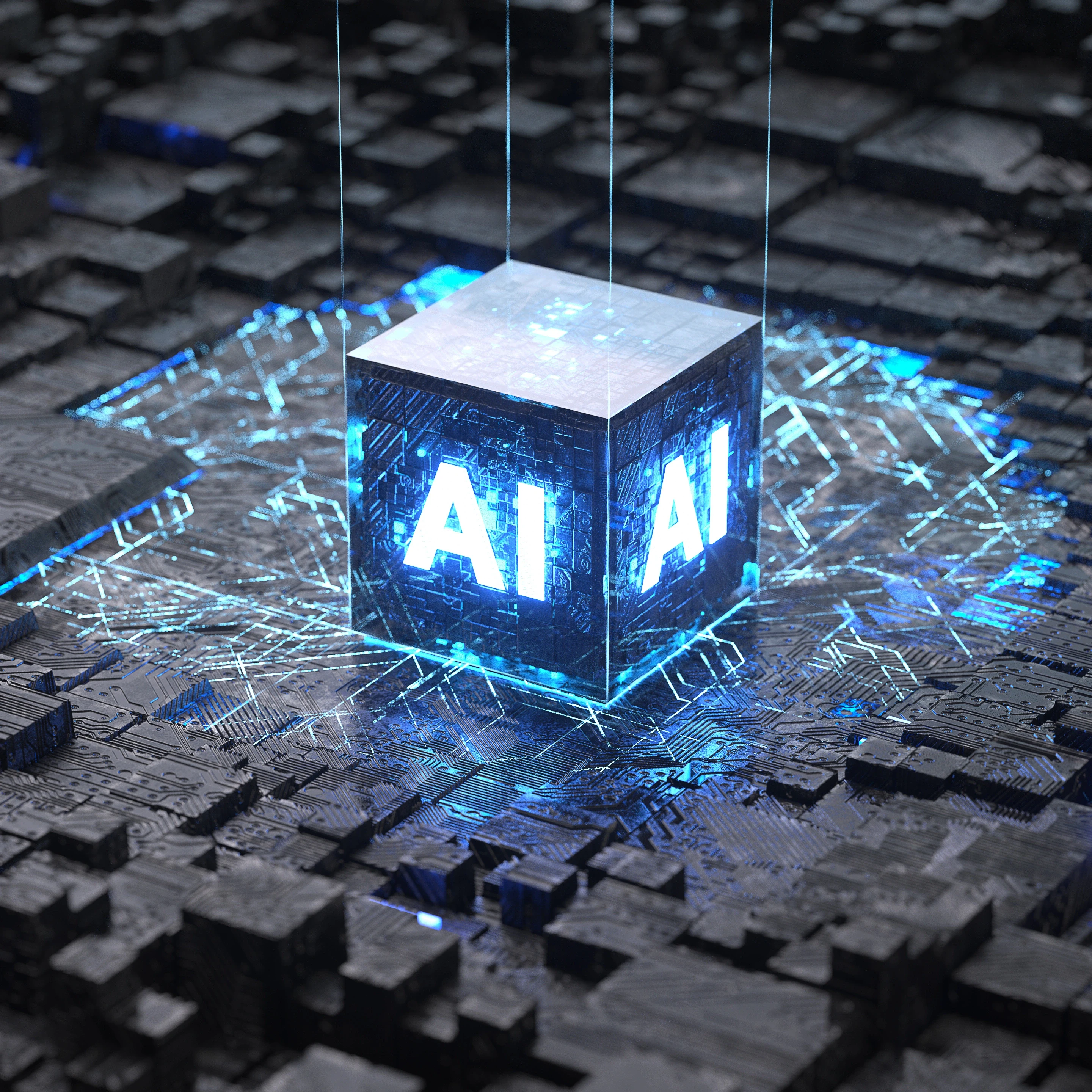
Challenges of the implementation of AI in manufacturing
Although the implementation of artificial intelligence in production as part of Industry 4.0 offers enormous benefits, it also brings with it a number of challenges. One of the biggest hurdles is the integration of AI systems into existing production processes, which can be complex and costly, especially in the electronics industry. High demands on precision and speed can make the use of AI more difficult, particularly when it comes to assembling printed circuit boards and manufacturing assemblies. In addition, there is often a lack of qualified specialists required to implement and maintain these systems. Companies must therefore invest in the training and further education of their employees. Another problem is data security, as AI systems require large amounts of data and are therefore susceptible to cyber-attacks. Robust security measures are therefore essential.
Employee acceptance is also a challenge, as many employees see artificial intelligence as a threat to their jobs. Transparent communication and the involvement of employees in the change process are crucial here. Finally, regulatory and ethical issues must also be clarified in order to comply with legal requirements and define responsibilities in the event of errors. Despite these challenges, the implementation of AI in manufacturing offers enormous potential for more efficient, more flexible and more sustainable production.
Although AI promises huge benefits for the manufacturing industry in the age of Industry 4.0, successful implementation comes with significant challenges. In fact, almost 9 out of 10 AI projects fail*1, and only a few of the use cases achieve a positive ROI. Here are the main reasons:
- Data connectivity issues: An astonishing 85% of potential assets remain unconnected, making it difficult for AI to fully optimize production.
- Streetlight effect: Many AI initiatives fail due to lack of alignment, focusing on irrelevant or low-impact production applications.
- Scalability hurdles: Developing an AI model is only part of the solution. The real challenge lies in scaling and integrating AI across complex production environments. As highlighted in the Gartner report “The Pillars of a Successful Artificial Intelligence Strategy”,*2 the AI strategy only becomes truly effective when it is aligned with the business strategy and other technology areas such as IT and data and analytics platforms. Successful scaling therefore requires not only the technological foundation, but also a clear operational model that enables the adoption of AI across the organization.
These obstacles, coupled with the complexity of integrating AI into existing production lines – particularly in precision industries such as electronics – make the successful deployment of AI a challenging task.
In addition, factors such as the lack of skilled professionals, data security concerns and the need for robust cybersecurity further complicate the adoption of AI. Companies also face the problem of resistance from the workforce, as many employees see AI as a threat to their jobs. Here, transparent communication and inclusive change management are crucial to address these concerns.
Finally, regulatory and ethical issues must also be clarified to ensure that AI systems comply with legal requirements and that responsibilities for errors are clearly defined. Despite these challenges, the implementation of AI in manufacturing offers enormous potential for more efficient, flexible and sustainable production.
Best practices and outlook for the use of AI in production
To fully harness the benefits of Artificial Intelligence in production, companies should define clear goals and adopt a gradual approach. Pilot projects can help test and refine the technology before making widespread changes. High-quality data is essential, as AI systems rely on clean, complete, and up-to-date information. Close collaboration between IT and production teams ensures that AI solutions are seamlessly integrated and meet specific requirements. Additionally, companies should invest in employee training to ensure that staff can effectively use the new technologies. Continuous monitoring and optimization of AI systems are also crucial to maintain their efficiency and effectiveness. By following these best practices, companies can successfully implement AI in manufacturing and fully unlock the potential of the technology.
In summary, AI in manufacturing enhances the accuracy and efficiency of anomaly detection, quality control, and process optimization. By leveraging machine learning and data analysis, manufacturers can achieve higher product quality, reduce downtime, and optimize resource utilization. Continuous learning and adaptation of AI systems ensure that manufacturing processes stay up-to-date, competitive, and meet stringent quality standards. The future outlook for AI in production is promising, as advanced algorithms and technologies continue to evolve, enabling even more precise predictions and automation. This will not only boost efficiency but also open new opportunities for innovation and tailored production solutions.
Further reading
The development of meaningful AI applications is still ongoing. But it is already clear: The use of AI in production goes far beyond hype and opens up new dimensions for Industry 4.0.
Find out how we use artificial intelligence in our solutions and how Gartner defines “The Pillars of a Successful Artificial Intelligence Strategy”:
*1 Ryseff, James, Brandon De Bruhl, and Sydne J. Newberry. "The Root Causes of Failure for Artificial Intelligence Projects and How They Can Succeed: Avoiding the Anti-Patterns of AI."
*2 Gartner, The Pillars of a Successful Artificial Intelligence Strategy, Pieter den Hamer, Raghvender Bhati, Apirl 23, 2024
GARTNER is a registered trademark and service mark of Gartner, Inc. and/or its affiliates in the U.S. and internationally and is used herein with permission. All rights reserved.