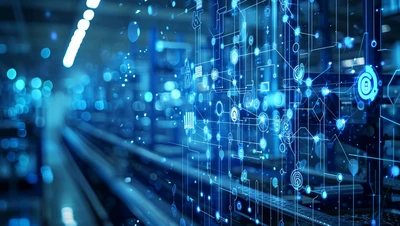
OEE那些不为人知的小秘密
为什么仅仅依靠OEE会无法达到工厂要的效果,以及如何解决这个问题?
如果您在制造业工作,您的工厂很可能是依赖关键绩效指标(KPI)来管理和优化生产,而其中之一就是设备综合效率 (OEE)。这个关键指标标示了设备性能,通常被用作整体生产效率的衡量维度。它将可用性、性能和质量整合为一个百分比数值。
然而,如果您在车间或生产管理部门工作过相当一段时间,您就可能了解OEE的实际局限性。传统OEE系统只关注设备利用率,忽略了人为因素、瓶颈、供应链延误和流程低效。OEE还经常被用于评估其设计初衷之外的流程,从而导致误导性结论和错失改进机会。如果不考虑这些更广泛的问题,OEE就无法全面反映生产绩效。在此,我将讨论为什么OEE可能并非灵丹妙药,以及基于软件的现代方法如何有效克服其局限性。
传统OEE软件的常见问题
制造业的OEE: 行业通常如何计算OEE
OEE是衡量设备或生产线生产率的关键数字。要计算整体设备效率,三个主要组成部分是可用性、性能和质量。通常使用以下公式将它们计算得到OEE:
OEE =可用性x生产效率x直通率
这只是一个数字,但不是故事的全部
OEE过度简化了运营,提供的是一个可能掩盖了实际问题的高层次视图。良好的OEE数据并不一定意味着流程没有问题,而可能是掩盖了一些问题,如与产品相关的质量问题或潜在的流程低效。
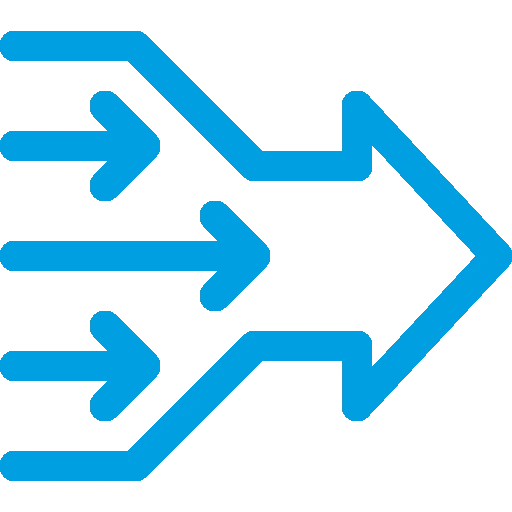
OEE可能损害整体效率
最大化OEE将资源利用率置于流程效率之上,可能反而降低整个流程速度。OEE 只关注设备性能,而不考虑整个工作流程的效率。优化单个设备可能反而导致整体效率降低,这就是 “效率悖论 ”的例证。*
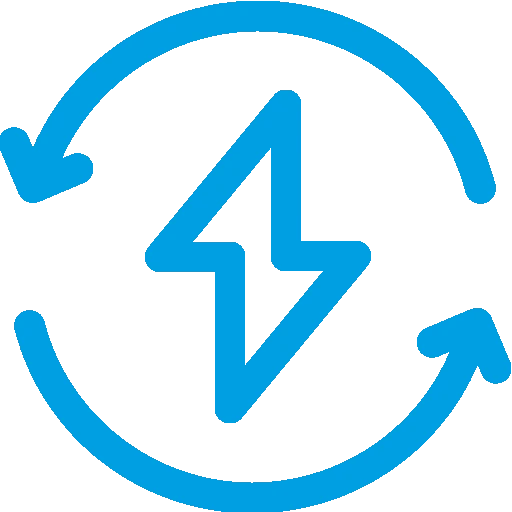
数据仅是"理论上"准确
虽然OEE的计算被认为是精确的,但其数据收集过程往往不一致,容易出现人为错误或操纵行为。不同班次的人员对事件可能有各种做法,从而导致数据不可靠并误导了结论。对局部条件的调整会进一步降低透明度,从而难以比较不同设备、生产线或现场的绩效。
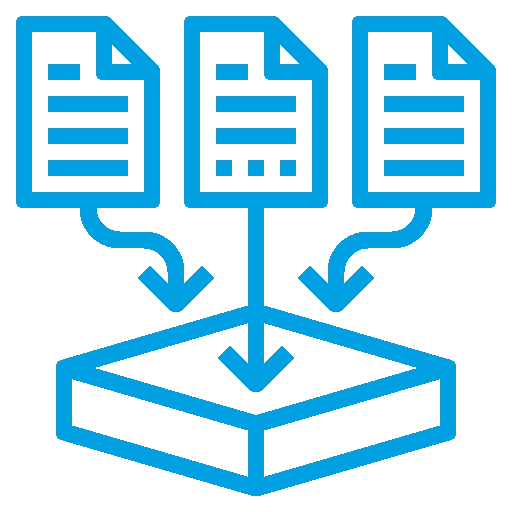
手动输入的效果取决于现场管理纪律
人工数据录入容易出错,需要管理人员强力落实,才能确保数据的质量。更好的设备集成可以使采集标准化,自动化, 但成本高昂,而且不容易扩展到各式各样的设备中。因此,许多系统仍然依靠耗时、不可靠和昂贵的人工输入。

集成和维护成本高昂
建立和维护一个测量生产效率和提高 OEE 的系统可能既昂贵又繁琐。通常需要将设备与系统(如 ERP、MES 和 APS)集成,并在传感器、连接性和软件方面进行大量投资。成本的增加可能意味着细节操作或低优先级的步骤可能被排除在外。维护这些系统还需要专门的人员,这进一步增加了运营成本。
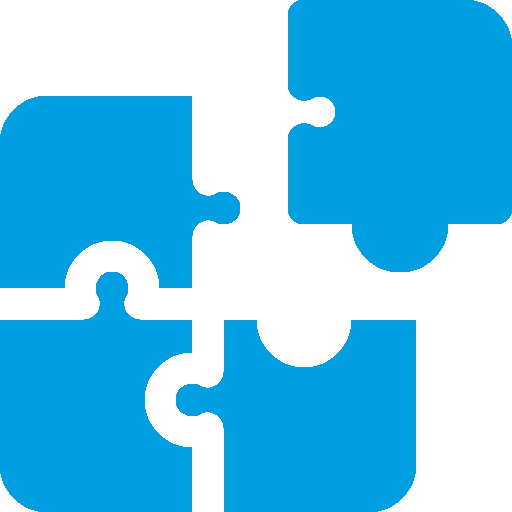
被动而非主动
传统的 OEE 系统主要是回顾性的,在问题发生后才进行分析。由于操作员只能在导致不必要的停机后将报警升级, 才能解决问题,因此几乎没有采取预防措施的余地。
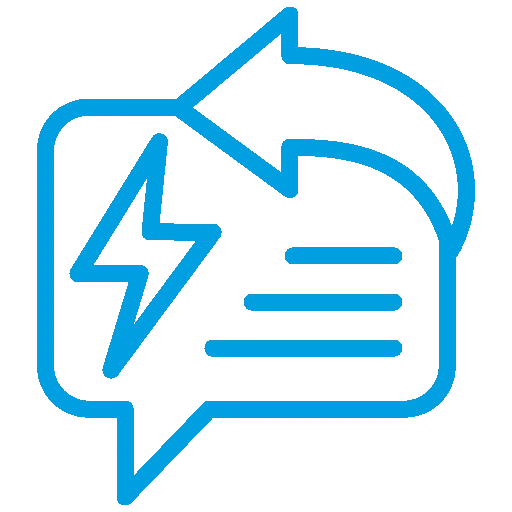
短期捷径重于长期方案
操作员甚至可能会以牺牲适当维护为代价来提高 OEE 数据。虽然短期效益看似惊艳,但可能导致长期故障和更高的成本。
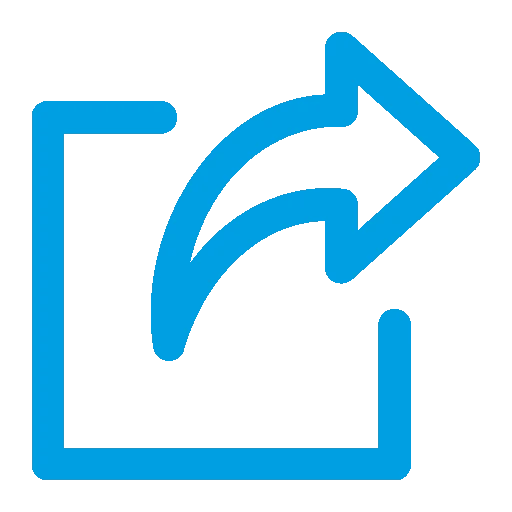
对人为因素的忽略
传统的OEE 系统无法仿效操作员的现场洞察力和专业知识。尤其是在人员流动率高、熟练劳动力稀缺的环境中,这种疏忽会导致宝贵的知识经验流失,阻碍持续改进。
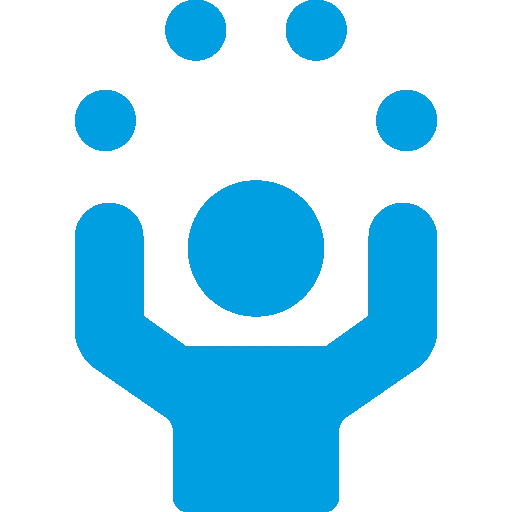
21世纪的OEE方法
鉴于这些挑战,我们不禁要问,在当今互联世界中,传统的 OEE 方法对于提高整体生产效率是否仍然实用。基于人工智能(AI)和设备学习(ML)的现代软件工具使我们能够定义新的资源优化范例,这些工具在数据测量和上下关联方面提供了更大的灵活性,并给予了一种全面的方法来改善生产设施,更易于使用及维护,也降低了操作的复杂性。下面,我将以 iTAC.IOT&AI为例,展示这种现代化的 OEE 方法。
解决设备连接难题
与传统的 OEE 系统不同,现代软件工具使用人工智能和 设备学习方法直接从设备数据流中推断参数状态。 iTAC.IOT&AI可自动分析历史数据,推断班次利用率、生产换型和计划外停机等因素,且无需对每种产品类型进行大量配置或人工干预。
简易的连接使这些系统实施起来更快、更省钱,比传统的大数据分析和 OEE 系统更快提供可利用的见解。这种现代化的方法可以解决制造商面临的 “连接难题 ”*:
- 避免与 MES、ERP 和计划系统进行昂贵集成。
- 减少手动配置带来的错误和不一致。
- 最大限度地减少用人工干预来维护数据源的需要。
- 降低结果被篡改的风险。
采用实时监控并主动触发工作流
现代工具提供实时分析,对问题做出即时响应。iTAC.IOT&AI可在潜在问题出现时通知团队,从而阻止停机并提高整体效率。因此,操作从被动反应转变为主动出击,缺陷、故障或异常测量值皆能触发自动响应。
利用虚拟双胞胎技术
人工智能驱动的虚拟生产线,分析设备在不断变化的条件下如何互动。iTAC IOT&AI的停机时间跟踪器可识别瓶颈、上游或下游问题及其对生产线整体性能的影响。这种全面的视角有助于做出更好的决策、更有效地利用资源。
整合人的洞察力
底线
虽然 OEE 是一个有用的指标,但它并不是提高现代制造业效率的最终解决方案。今天的工厂需要的工具不仅要考虑设备性能,还要考虑流程效率、实时监控和人类的专业知识。人工智能驱动的系统提供了一种更实用、更有效的方法,它将数据、上下文和前瞻性策略结合在一起,推动车间发生有意义的变化。真正的生产力不是追求高 OEE 分数,而是通过更智能的集成解决方案实现可持续改进。
*延伸阅读
Liker, J.K., 2004. The Toyota way; The company that invented lean production.
Modig, N. and Åhlström, P., 2012. This is lean: Resolving the efficiency paradox. Vol. 41. Stockholm: Rheologica.
Riggs, J.L., 1987. Production systems: planning, analysis, and control. Vol. 582. New York: Wiley.
Toro, C., Wang, W. and Akhtar, H., 2021. Implementing Industry 4.0. Springer International Publishing.
Womack, J.P., Jones, D.T. and Roos, D., 2007. The machine that changed the world: The story of lean production--Toyota's secret weapon in the global car wars that is now revolutionizing world industry. Simon and Schuster.