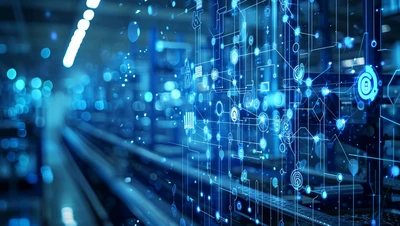
Das Geheimnis von Overall Equipment Effectiveness (OEE)
02.12.2024
Warum es fatal ist sich in Ihrer Fabrik nur auf die OEE-Kennzahl zu verlassen
Wenn Sie in der Fertigung arbeiten, ist die Gesamtanlageneffektivität (engl. OEE) wahrscheinlich einer der Leistungskennzahlen (KPIs), auf die sich Ihre Fabrik zur Optimierung der Produktion stützt. Diese nützliche Kennzahl wird herangezogen, um die Gesamtanlageneffektivität zu berechnen. Sie bietet eine Momentaufnahme der Maschinenleistung und wird häufig als Ersatzgröße zur Messung der Gesamtproduktionseffizienz verwendet. Zur OEE-Berechnung werden die Faktoren Verfügbarkeit, Leistung und Qualität herangezogen und in einer einzigen prozentualen Zahl kombiniert.
Wenn Sie jedoch viel Zeit in der Werkstatt oder im Produktionsmanagement verbracht haben, kennen Sie wahrscheinlich die praktischen Grenzen der OEE-Berechnung. Durch die ausschließliche Konzentration auf die Auslastung der Anlagen ignorieren traditionelle OEE-Richtwerte menschliche Faktoren, Engpässe, Verzögerungen in der Lieferkette und Prozessineffizienzen. OEE-Daten werden auch häufig zur Bewertung von Prozessen verwendet, für die sie nicht konzipiert wurde, was zu irreführenden Schlussfolgerungen und verpassten Verbesserungsmöglichkeiten führt. Ohne Berücksichtigung dieser umfassenderen Aspekte liefert die OEE-Betrachtung ein unvollständiges Bild vom Leistungsgrad der Produktion. In diesem Artikel wird erläutert, warum eine reine OEE-Optimierung nicht die Lösung ist und wie moderne softwarebasierte Ansätze ihre Grenzen effektiv überwinden können.
Häufige Probleme mit herkömmlichen Systemen zur OEE Analyse
Was ist OEE?
Die OEE ist eine Kennzahl, die die Produktivität einer Maschine oder Produktionslinie misst. Um die Gesamtanlageneffektivität zu berechnen werden die drei Hauptfaktoren Verfügbarkeit, Leistungsgrad und Qualitätsrate berücksichtigt.
Formel zur OEE-Berechnung: Verfügbarkeit x Leistungsgrad x Qualitätsrate
Es ist nur eine Zahl, nicht die ganze Geschichte
Die Gesamtanlageneffektivität (OEE) vereinfacht die Betriebsabläufe zu sehr und bietet einen allgemeinen Überblick, der echte Probleme verschleiern kann. Ein guter OEE-Wert bedeutet nicht unbedingt, dass der Prozess störungsfrei ist, und könnte Probleme wie produktbezogene Qualitätsprobleme oder zugrunde liegende Prozessineffizienzen verbergen.
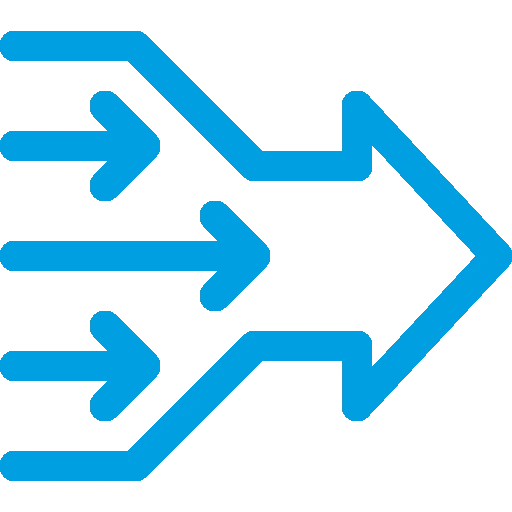
OEE kann die Gesamteffizienz tatsächlich beeinträchtigen
Die Maximierung der OEE-Kennzahl kann das System paradoxerweise verlangsamen, indem die Ressourcennutzung über die Effizienz des Materialflusses gestellt wird. Overall Equipment Effectiveness konzentriert sich ausschließlich auf die Maschinenleistung, ohne die Effizienz der Arbeit zu berücksichtigen, die durch den gesamten Prozess fließt. Die Optimierung einzelner Maschinen kann die Gesamtsystemeffizienz verringern, was das „Effizienzparadoxon“ veranschaulicht.*
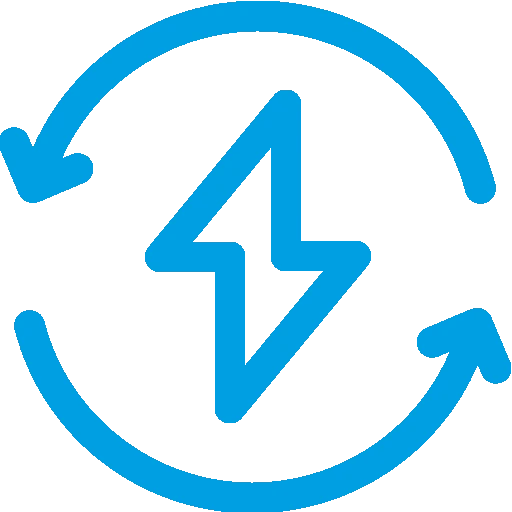
Genaue Daten? Nur in der Theorie
Die OEE-Berechnung gilt zwar als präzise, doch der Prozess der Datenerfassung ist oft inkonsistent und anfällig für menschliche Fehler oder Manipulationen. Verschiedene Personalschichten oder Mitarbeitende können Ereignisse unterschiedlich interpretieren, was zu unzuverlässigen OEE-Daten und irreführenden Ergebnissen führt. Anpassungen an lokale Bedingungen verringern die Transparenz weiter und erschweren den Vergleich der Leistung zwischen Maschinen, Produktionslinien oder Standorten.
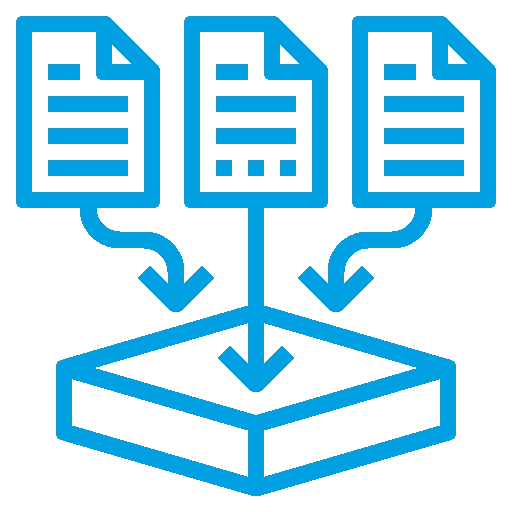
Manuelle Eingaben sind nur so gut wie die Disziplin des Managements
Manuelle Dateneingaben sind fehleranfällig und inkonsistent und erfordern viel Disziplin des Managements, um eine gute Datenqualität zu gewährleisten. Eine bessere Maschinenintegration kann Eingaben standardisieren, ist jedoch kostspielig und lässt sich in Einrichtungen mit unterschiedlicher Hardware nicht gut skalieren. Daher werden in vielen Systemen immer noch manuelle Eingaben verwendet, die zeitaufwendig, unzuverlässig und teuer sind.

Hohe Kosten für Integration und Wartung
Die Einrichtung und Wartung eines Systems zur OEE-Berechnung und OEE-Analyse kann kostspielig und mühsam sein. Oftmals müssen Maschinen in Datensysteme (wie ERP, MES und APS) integriert werden und es sind hohe Investitionen in Sensoren, Konnektivität und Software erforderlich. Steigende Kosten können dazu führen, dass kleinere Betriebe oder weniger kritische Schritte ausgeschlossen werden. Die Wartung dieser Systeme erfordert außerdem dediziertes Personal, was die Betriebskosten weiter erhöht.
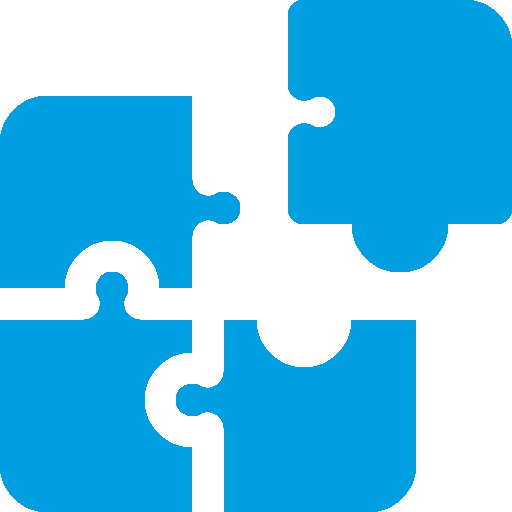
Reaktiv, nicht proaktiv
Traditionelle Systeme zur OEE-Betrachtung sind in erster Linie rückblickend und analysieren Probleme, nachdem sie aufgetreten sind. Dies lässt wenig Spielraum für vorbeugende Maßnahmen, da Bediener Probleme erst angehen können, nachdem sie eskaliert sind und unnötige Ausfallzeiten oder Ineffizienzen verursacht haben.
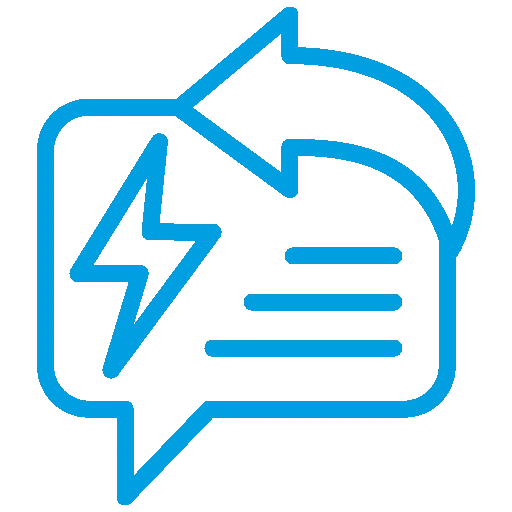
Shortcuts statt Lösungen
Betreiber könnten sogar versuchen, die OEE-Richtwerte auf Kosten einer ordnungsgemäßen Wartung oder nachhaltiger Praktiken zu steigern. Kurzfristige Gewinne mögen zwar beeindruckend aussehen, können aber langfristig zu Ausfällen und höheren Kosten führen.
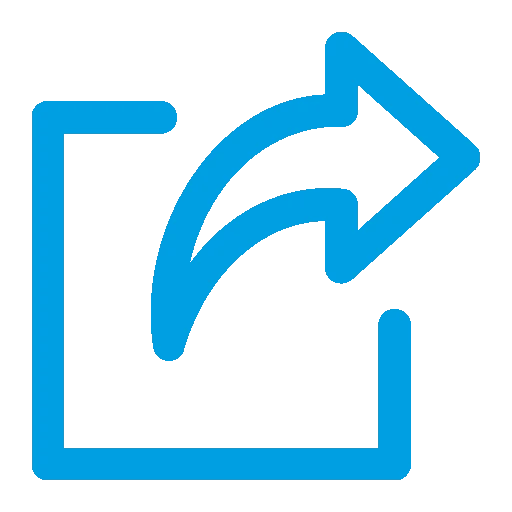
Ignoriert den Faktor Mensch
Traditionelle OEE-Richtwerte erfassen nicht die Erkenntnisse und das Fachwissen menschlicher Bediener. Diese Auslassung verhindert eine kontinuierliche Verbesserung und ignoriert wertvolles Wissen, insbesondere in Umgebungen mit hoher Fluktuation und einem Mangel an qualifizierten Arbeitskräften
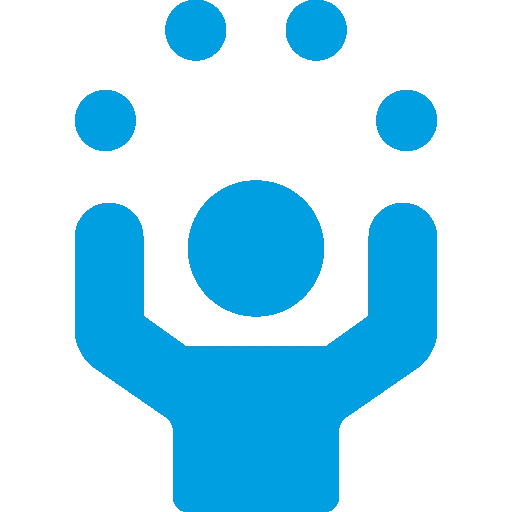
OEE AI: Der Ansatz des 21. Jahrhunderts für die Gesamtanlageneffektivität
Angesichts dieser Herausforderungen stellt sich die Frage, ob der traditionelle Ansatz der Gesamtanlageneffektivität in der heutigen vernetzten Welt noch praktikabel ist, um die Gesamteffizienz der Produktion zu verbessern. Moderne Softwaretools, die auf Künstlicher Intelligenz (KI) und Maschinellem Lernen (ML) basieren, ermöglichen es uns, neue Paradigmen für die Ressourcenoptimierung zu definieren. Diese Tools sind benutzer- und wartungsfreundlicher, bieten mehr Flexibilität bei der Messung und Kontextualisierung von Daten und ermöglichen einen ganzheitlichen Ansatz zur Verbesserung von Produktionsanlagen bei gleichzeitiger Reduzierung der betrieblichen Komplexität. Im Folgenden wird dieser moderne Ansatz für die OEE-Optimierung am Beispiel des iTAC.Asset.Analyzer veranschaulicht.
Vereinfachung Ihres Konnektivitätsproblems
Im Gegensatz zu herkömmlichen Systemen zur OEE-Betrachtung und OEE-Analyse verwenden moderne Softwaretools KI- und ML-Methoden, um Systemparameter direkt aus Maschinendatenströmen abzuleiten. Der iTAC.Asset.Analyzer analysiert automatisch historische Daten, um Faktoren wie Schichtauslastung, Produktwechsel und ungeplante Ausfälle abzuleiten, und benötigt keine umfangreiche Konfiguration oder manuelle Eingriffe für jeden Produkttyp.
Durch die vereinfachte Konnektivität lassen sich diese Systeme schneller und kostengünstiger implementieren und liefern viel früher umsetzbare Erkenntnisse als herkömmliche Business-Intelligence- und OEE-Systeme. Dieser moderne Ansatz löst das „Konnektivitätsproblem“*, mit dem Hersteller konfrontiert sind. Die OEE-Berechnung wird damit obsolet:
- Vermeidet kostspielige Integration mit MES-, ERP- und Planungssystemen.
- Reduziert Fehler und Inkonsistenzen, die durch manuelle Konfiguration entstehen.
- Minimiert die Notwendigkeit menschlicher Eingriffe zur Pflege von Datenquellen.
- Verringert das Risiko von Ergebnismanipulationen.
Abbildung 1: Normalerweise ist eine beträchtliche Menge zusätzlicher Daten erforderlich, um mit den traditionellen Methoden die Maschinenverfügbarkeit zu berechnen, was zu kostspieligen Integrationsbemühungen mit dem ERP- und Planungstool einer Fabrik führt, die automatisiert werden sollen. Oben sehen wir ein Beispiel dafür, wie moderne Tools Schlüsselparameter auf intelligente Weise aus vorhandenen Maschinendaten ableiten können, ohne dass mehrere Systeme integriert werden müssen. Im oberen Diagramm sehen wir, wie das System automatisch die geplante produktive Zeit (PT) und die nicht produktive Zeit (NPT) identifiziert hat. Im unteren Diagramm sehen wir, wo die KI automatisch Umstellungen in der Produktionslinie erkannt hat, wobei jedes Produkt in einer anderen Farbe dargestellt ist. Dies hat auch den zusätzlichen Vorteil, dass viele menschliche Eingriffe und unnötige manuelle Dateneingaben entfallen und Fehler minimiert werden.
Einführung von Echtzeitüberwachung und Workflow-Triggern
Moderne Tools bieten Echtzeitanalysen und ermöglichen so eine sofortige Reaktion auf Probleme. Der iTAC.Asset.Analyzer benachrichtigt Teams über potenzielle Probleme, sobald sie auftreten, wodurch Ausfallzeiten vermieden und die Gesamteffizienz verbessert werden. Der Betrieb wird dadurch von reaktiv auf proaktiv umgestellt und Alarme, Fehler oder Ausreißermessungen können als Auslöser für automatisierte Reaktionen verwendet werden.
Abbildung 2: Das System iTAC.Asset.Analyzer erkennt automatisch anomales Systemverhalten, indem es Messdaten überwacht und Ausreißer im Datensatz in Echtzeit erkennt. Diese können verwendet werden, um Alarme einzustellen oder Workflows auszulösen, wenn bestimmte Schwellenwerte erreicht werden.
Abbildung 3: Ein Beispiel für eine automatische Nachricht, die vom iTAC.Asset.Analyzer an das Schichtteam der Verfahrenstechnik gesendet wurde, um ein Problem an der Conformal Coating Inspection (CCI)-Maschine zu untersuchen, nachdem eine ungewöhnlich hohe Häufung von Qualitätsproblemen festgestellt wurde. Hier wird ein externer Workflow ausgelöst, bei dem das Team über MS Teams über das anomale Verhalten und die hinderliche Situation informiert wird..
Nutzung der Virtual-Twins-Technologie
KI-gestützte virtuelle Modelle simulieren Produktionslinien und analysieren, wie Maschinen unter sich ändernden Bedingungen interagieren. Der Downtime Tracker des iTAC.Asset.Analyzer identifiziert Engpässe sowie vor- oder nachgelagerte Probleme und deren Auswirkungen auf die Gesamtleistung der Linie. Diese ganzheitliche Sichtweise fördert eine bessere Entscheidungsfindung und eine effektivere Ressourcennutzung.
Abbildung 4: Moderne Tools verstehen nicht nur die Dynamik jeder Maschine, sondern auch, wie das Verhalten aller Maschinen in der Produktionslinie in bestimmten Situationen, wie z. B. bei Ausfällen, voneinander beeinflusst wird. Oben sehen wir, wie der iTAC.Asset.Analyzer digitale Zwillingsmodelle verwendet, um den Echtzeit-Datenstrom zu erweitern und sehr genaue Zustandsrepräsentanten jeder Maschine und den Gesamtstatus der Produktionslinie bereitzustellen. Diese geben dem Produktionspersonal ein tieferes Verständnis für die Ursachen von Produktionsausfällen und einem reduzierten Leistungsgrad der Produktion.
Abbildung 5: Die Echtzeit-Verfolgung des iTAC.Asset.Analyzer verwendet eine Effizienzmatrix[1], um den Systembenutzern zu zeigen, wie effizient einzelne Ressourcen in einer Produktionslinie genutzt werden und wie viel sie zur gesamten Flusseffizienz beitragen. Der perfekte Zustand sind Maschinen, die sowohl effizient als auch schlank laufen, was in der oberen linken Ecke der Matrix dargestellt wird. „Efficient Islands“ oder Maschinen, die isoliert, aber nicht in Bezug auf andere Maschinen in der Linie effizient laufen, werden in der oberen rechten Ecke dargestellt. „Efficient Oceans“, d. h. Maschinen, die synchron miteinander laufen, aber nicht ausgelastet sind, befinden sich in der unteren rechten Ecke. Maschinen in der Kategorie „Wasteland“ (unten links) sind nicht ressourcen- oder flusseffizient und stellen das unerwünschteste Szenario dar. In diesem Beispiel sehen wir, dass die Engpassmaschine (pnp_2) unterhalb der maximalen Ressourceneffizienz läuft. Diese Situation ist nicht ideal, und das Management kann sofort erkennen, dass es in der gesamten Linie enorme potenzielle Produktivitätssteigerungen gibt, wenn die Auslastung dieser einen Maschine verbessert werden kann.
Integration menschlicher Erkenntnisse
Ein innovatives System wie das iTAC.Asset.Analyzer AI Playbook erfasst menschliches Fachwissen, dokumentiert menschliche Handlungen, um deren Ursachen zu ermitteln, und gibt sogar umsetzbare Empfehlungen ab. Dies hilft Teams, aus vergangenen Herausforderungen zu lernen, proaktive Lösungen zu entwickeln und ihre Leistung kontinuierlich zu verbessern. Vollständig integrierte Connected-Worker-Lösungen wie diese befähigen KI der nächsten Generation, beispiellose Effizienzsteigerungen zu erzielen.
Abbildung 6: Ein Beispielmenü aus dem iTAC.Asset.Analyzer, das es den Bedienern ermöglicht, während des Problemlösungsprozesses zusätzliche Kommentare hinzuzufügen, sodass ihr Prozesswissen und ihre Werkskenntnisse mit Echtzeit-Datenströmen zusammengeführt werden können..
Fazit
Die Overall Equipment Effectiveness ist zwar eine nützliche Kennzahl, aber nicht die ultimative Lösung zur Effizienzsteigerung in der modernen Fertigung. Die Fabriken von heute benötigen Tools, die über die Maschinenleistung hinausgehen und auch die Effizienz des Materialflusses, die Echtzeitüberwachung und das Fachwissen des Menschen berücksichtigen. KI-gesteuerte Systeme bieten einen praktischeren und effektiveren Ansatz, indem sie Daten, Kontext und proaktive Strategien kombinieren, um sinnvolle Veränderungen in der Fertigung voranzutreiben. Bei echter Produktivität geht es nicht darum, eine OEE Optimierung zu erzielen oder die Maschinenverfügbarkeit zu berechnen, sondern nachhaltige Verbesserungen durch intelligentere, integrierte Lösungen zu erreichen.
*Literatur
Liker, J.K., 2004. The Toyota way; The company that invented lean production.
Modig, N. and Åhlström, P., 2012. This is lean: Resolving the efficiency paradox. Vol. 41. Stockholm: Rheologica.
Riggs, J.L., 1987. Production systems: planning, analysis, and control. Vol. 582. New York: Wiley.
Toro, C., Wang, W. and Akhtar, H., 2021. Implementing Industry 4.0. Springer International Publishing.
Womack, J.P., Jones, D.T. and Roos, D., 2007. The machine that changed the world: The story of lean production--Toyota's secret weapon in the global car wars that is now revolutionizing world industry. Simon and Schuster.